ACT smart clean processor systems set themselves apart from others by incorporating the use of an elevator within each processing chamber. The elevator serves two purposes: first, and most importantly, it provides continuous oscillation to gently move parts throughout the ultrasonic cleaning area during processing, and second, it easily transports parts into and out of the cleaning chamber.
WHAT SETS THE ACT SMART CLEAN PROCESSORS APART FROM THE COMPETITION?
Purpose Built Cleaning System
ACT’s uniquely engineered systems provide controlled agitation with solution immersion, heat application, directed spray, rotation, detergency and even cavitation energy. 5,000-lb parts? Not an issue for ACT. Whatever sized production or overhaul parts that you have, we can build a purpose-built, modified or custom-designed system to meet your requirements.
Our systems can be configured to meet ASTM specifications, military requirements, strict cleanliness standards, passivation or even conversion coating and more!
Smart Clean Processor Systems Built with Simplified Maintenance in Mind
Unlike typical units, ACT provides the actual power rating of each system, ensuring owners get the high watt/gallon ratios our systems are known for. We build our systems with removal tank immersible and transducer for simplified maintenance.
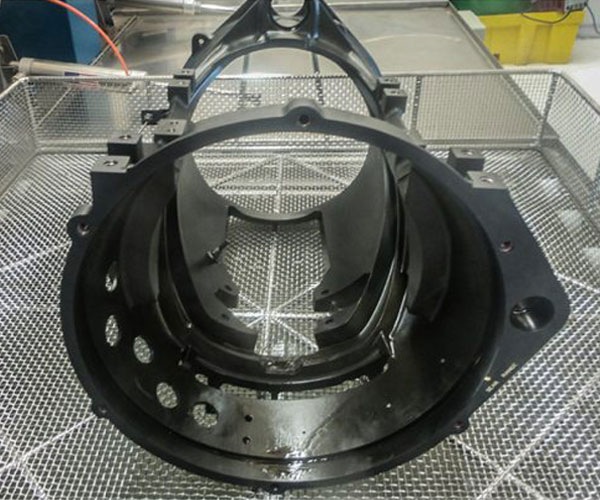
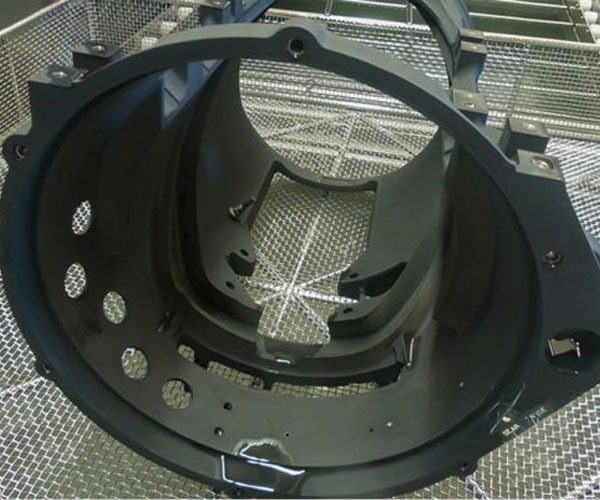
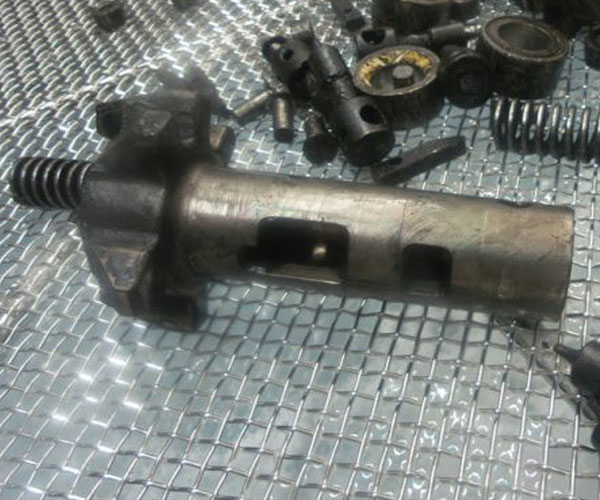
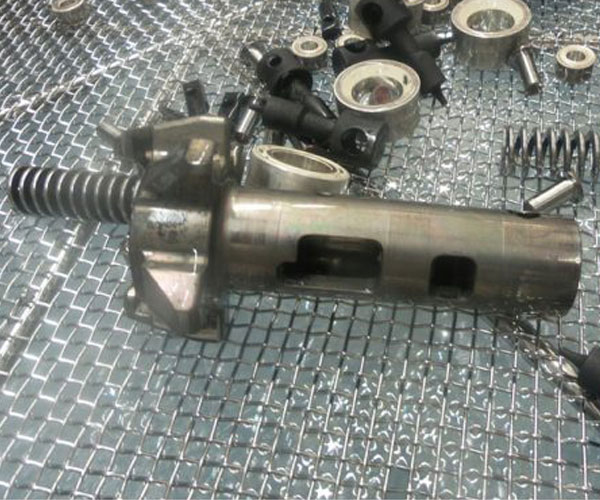
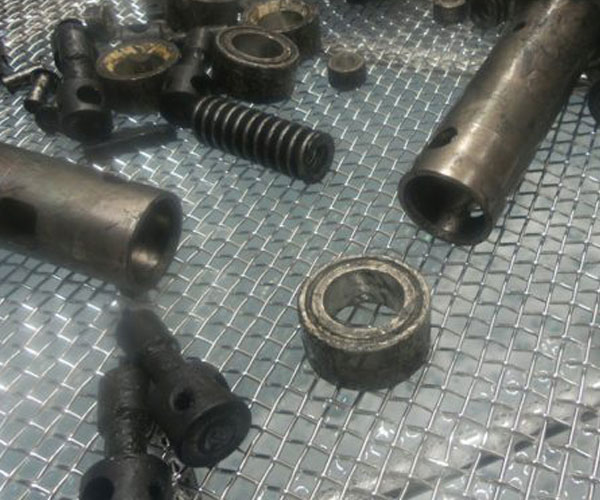

INNOVATIVE SMART CLEAN PROCESSOR STAGE COMBINATIONS
Turbulating Washing and Rinsing
Combining platform oscillation with turbulent immersion washing and rinsing produces continually changing flow patterns to provide an even flow of turbulence over, under, around and through components to help clean even the most complex parts.
Spraying
Our systems combine platform oscillation with pressure spray washing/rinsing results in constantly changing spray patterns to minimize shielding and increase coverage across all surfaces of the parts.
Ultrasonic
This stage also utilizes an oscillating platform to gently move the parts being cleaned across the ultrasonic working zone. Additionally, ultrasonic stages can be alternated with turbulating stages. This is an especially effective way to handle stubborn contaminants such as buffing or lapping compounds
Drying
Our drying stage uses high volume hot air combined with changing air flow patterns created by the oscillating elevator generates rapid parts drying without excessive heating.
Tired of Putting in Dirty Parts and Getting Wet Dirty Parts Back?
ACT immersion washers eliminate the toughest soils and contamination.
ENGINEERED TO SOLVE YOUR SPECIFIC INDUSTRIAL CLEANING APPLICATION
ACT engineers its systems with racks and fixtures that are built in-house to maximize sonic penetration to the load. Our systems deliver an alternating regimen of ultrasonics and gentle to aggressive (adjustable) agitation of the load at 20 to 240 strokes per minute.
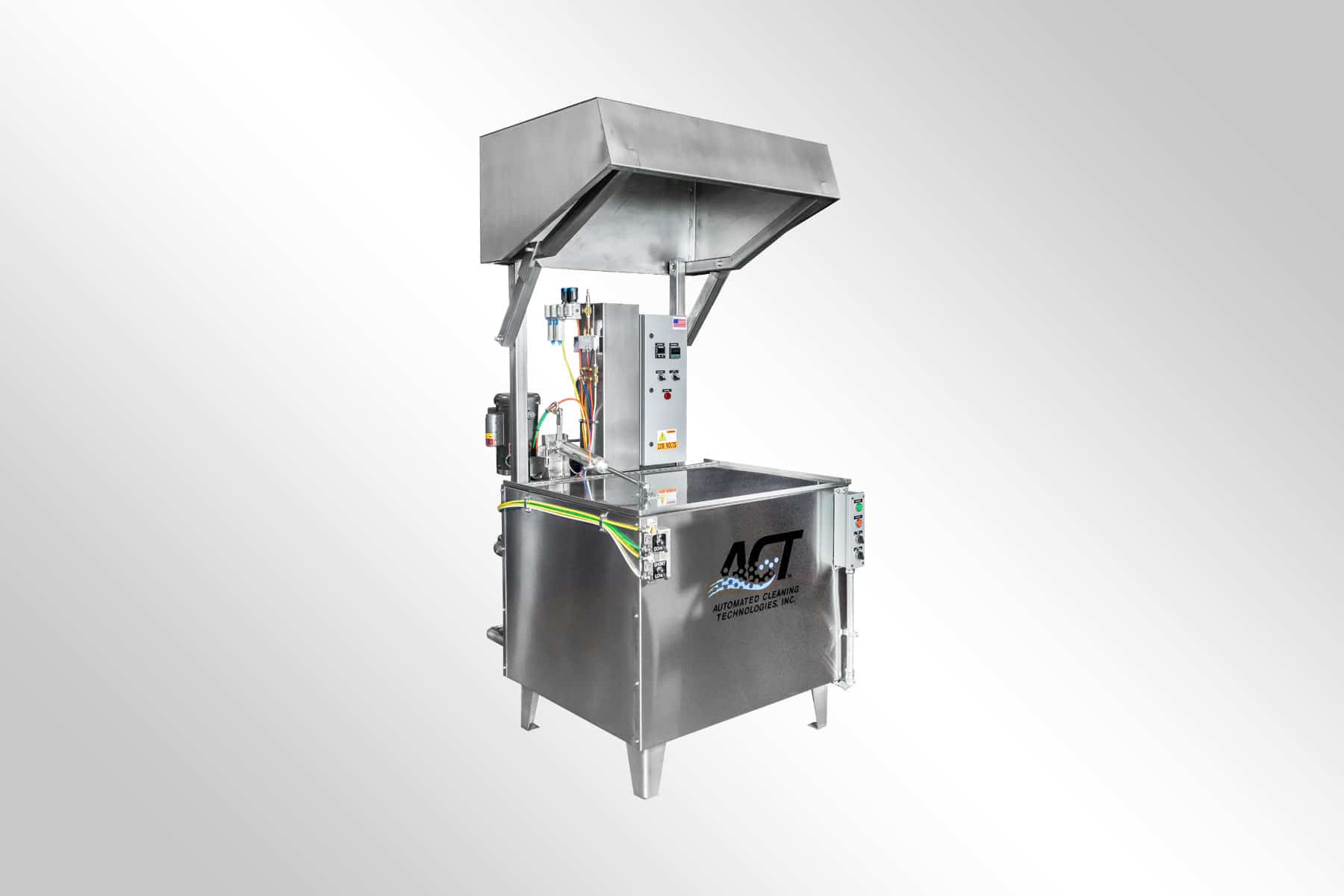
Vent Hood
Control Panel
Controls ultrasonics, timers, temperature, agitation and more
Vertical (Seal-Less) Pump
Allows for extended pump life and superior seal protection